スポンサーリンク
得られたデータをもとに分析をしていって、現状を把握し、対策の案を考えていくわけですが、この分析の手法が有名な”QC7つ道具”と呼ばれるものになります。簡単にその内容を説明します。ちなみに7つと言いながら、実は8つあります(笑)
①パレート図
下図のようにデータを項目ごとにまとめて、何がどの程度の割合で発生しているかなどをわかりやすくするもので、まず最初に改善すべき課題を明確にするときなどに使われます。下図の例で言えばまず最初に対策すべきは 歪み であることがわかります。
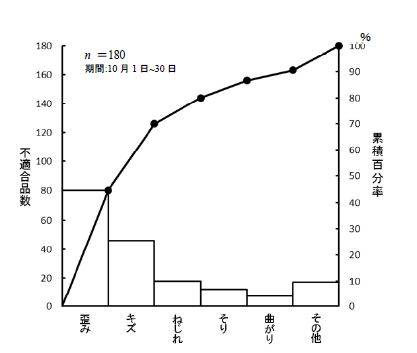
②特性要因図
魚の骨(フィッシュボーン)とも呼ばれ、ある結果(特性)に影響する要因をまとめたものになり、下図のようなイメージになります。これは例えば、ある不具合に影響しそうな項目を洗い出し、それをまとめていって作成します。この時先ほど出てきた5Mの視点をもって、関係者でブレーンストーミングなどを実施して作成するとよいでしょう。そして不具合などに対して、重要な要因と考えられるものに対して、対策を打っていくという使い方をします。
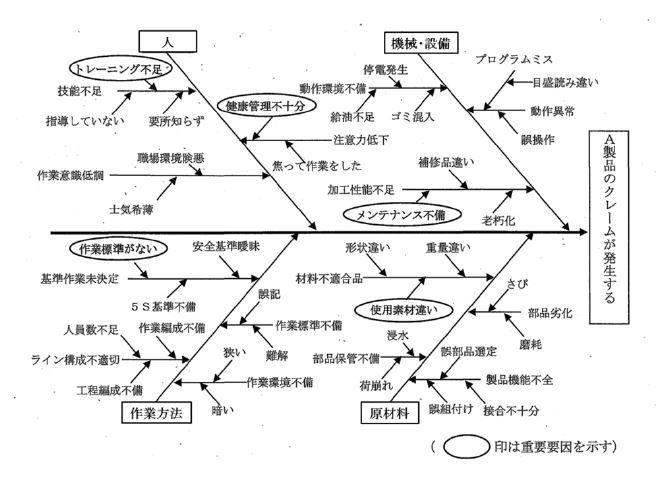
③ヒストグラム
ヒストグラムは棒グラフの一種ですが、データの範囲をいくつかに区分して、それぞれの区分にどれだけのデータがあるかを表したものになります。事例は下図のようになりますが、このようにすることによって、データのばらつき具合を目で見ることができるようになります。例えば下図ではばらつきが大きく下限を下回っていることがわかります。
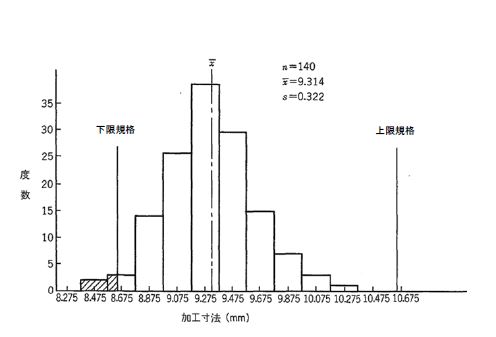
④グラフ
グラフはあまり説明の必要がないとは思いますが、いろいろな種類のグラフがあり、データを理解しやすくするうえで、適切なグラフの種類を選ぶ必要があります。すなわち何を伝えたいかによって、グラフの種類を選ぶことになります。
⑤管理図
管理図は一般的にプロセスの異常を検知するために用いられます。例えばある処理を行うための溶液があるとして、その溶液の比重を毎日はかって記録していくことにより、その変化の傾向を読み取ることができ、異常値になる前に比重を調整するなどの手当てをすることができます。
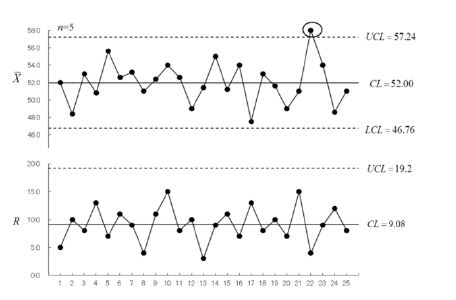
⑥チェックシート
チェックシートはデータを”記録するためのチェックシート”や、”確認をするためのチェックシート”があります。
例えばデータを”記録するチェックシート”は不良の種類をあらかじめ記載しておき、対応する不良の欄に個数を”正”の字などで記録しておくときに使用します。また”確認するためのチェックシート”は設備保全をするときの項目をあらかじめ記載しておき、その作業を実施したらチェックするというように使います。
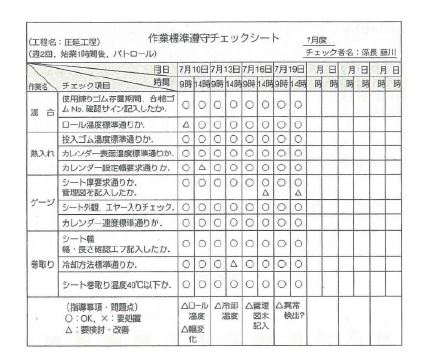
⑦散布図
散布図は二つの特性をX軸とY軸にとり、データを点でプロットしていって作ります。これによりデータの間にある関係性を見ることができます。例えばXの値が増えるとYの値も増える傾向が見られれば、この二つには正の相関性があるということになります。
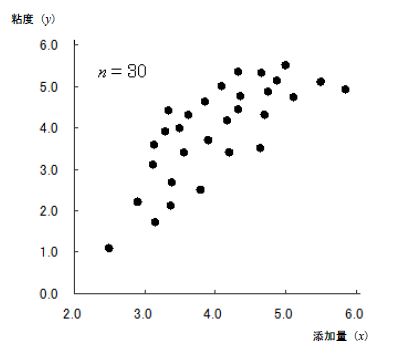
⑧層別
層別は母集団をいくつかの層で区切って分析することです。パレート図やヒストグラム、散布図など他の7つ道具と併用で使用することができます。
下図の例で言えば散布図との併用になりますが、全体の母集団ではよくわからない傾向だとしても、機械の1号機と2号機で層別することにより傾向が見えてくる事例です。
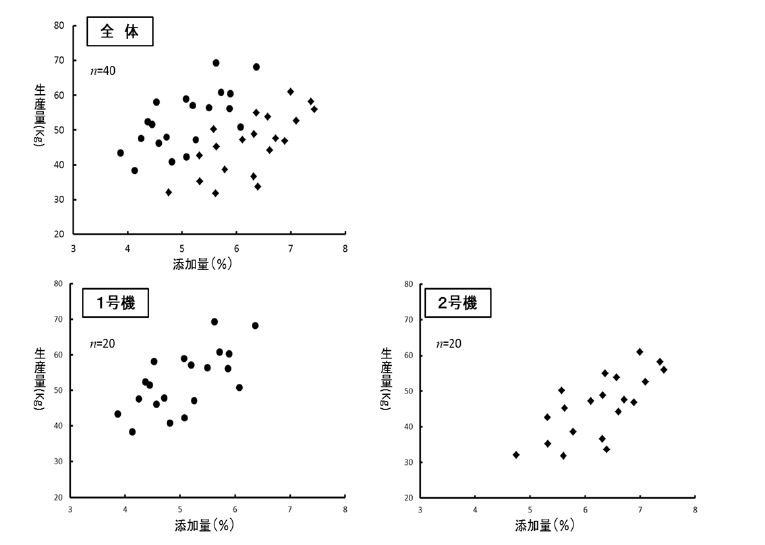
以上簡単にQC7つ道具を説明してきました。ところでQC7つ道具は事実に基づいて現状を正しく把握するための道具ですが、あくまで道具です。
本当に必要なのは、これらを用いて分析をした後、不具合や課題の原因を考えて対策を検討することになります。そして対策を実行し、その結果を確認して、対策が正しかったか?違ったら次に何をするかを考えて、再度対策を打ち、うまくいったら標準化して歯止めとすることになります。
スポンサーリンク